Your cart is currently empty!
11 Types of Kiln for Pottery – Different Kilns for Clay
Published:
Last Updated:
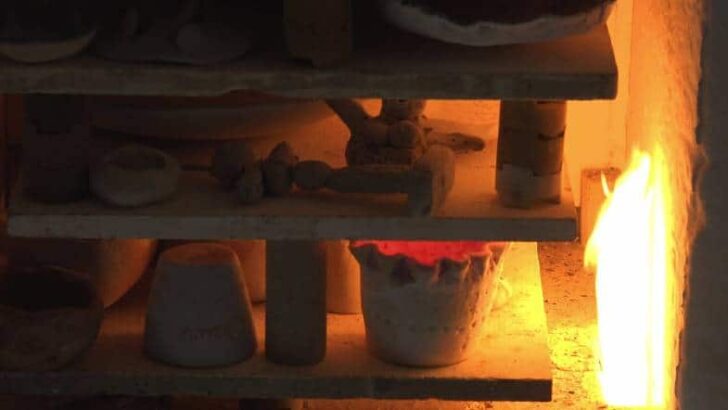
Affiliate Disclaimer
As an affiliate, we may earn a commission from qualifying purchases. We get commissions for purchases made through links on this website from Amazon and other third parties.
Kilns are insulated chambers that use fuel or electricity to reach high temperatures. When something is heated in a kiln it is described as being ‘fired’. There are different types of kiln to fire different materials. For example, there are kilns designed specifically for ceramics, glass, metal, brick, metal clay, and enamels.
This article is about the different types of kiln used for pottery and ceramics. There are lots of different types of kiln used in pottery. And the design of pottery kilns has developed over the years.
First, I will take a look at the different types of kiln that are commonly used by potters today. Then I will take a look at different types of kiln that have been used historically. This history is interesting in itself. But, it’s also relevant because many potters still use kilns that have an older more, traditional, or even primitive design.
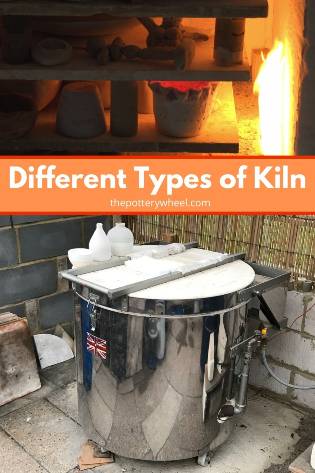
Contemporary Types of Kiln
Broadly speaking you can classify kilns that are used by modern potters along two lines. The first one is the way that the kiln is heated. Some kilns are heated by electricity. Other kilns are heated by burning fuel. These are known as fuel-burning kilns. The fuel used can range from natural gas, propane, wood, and sawdust. These are a few of the combustible materials used to heat a fuel-burning kiln.
The other distinction that is made in types of kiln is whether a kiln is continuous or intermittent. Most smaller kilns that are used by individual potters and hobby potters are intermittent or periodic kilns. These kilns are loaded with ware, turned on, heated, allowed to cool, and then unloaded.
By contrast, continuous kilns stay on. The ware is loaded onto a moving platform and travels through one side of the kiln and out the other. The kiln stays hot and the ware cools as it leaves the kiln. These kilns are more typical of commercial or industrial settings where very large amounts of ceramics are being made.
Amongst individual potters and hobby potters, electric kilns are most commonly used. However, gas kilns are also a common way of firing pottery. And gas kilns have been around longer than electric kilns. So, let’s take a look at gas kilns first.
1) Gas Kilns
Gas kilns use either natural gas or propane. The kiln consists of a chamber that is insulated with fire bricks. Heat is introduced to the chamber by burner ports at the base of the kiln. Burner ports are basically openings through which lit gas passes. Gas kilns either have an updraft or a downdraft design.
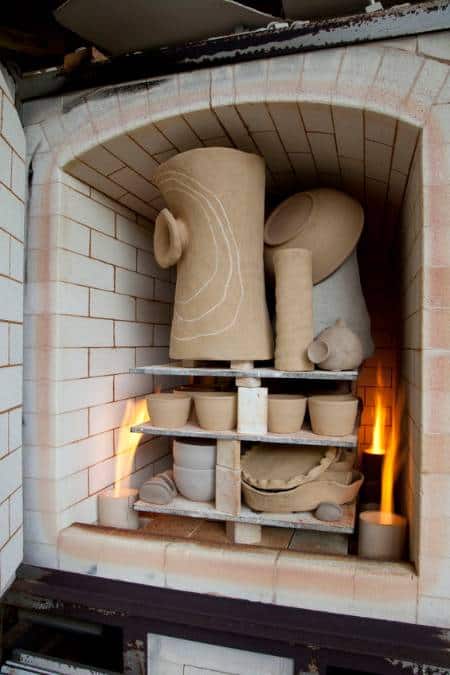
Updraft kilns
Typically, updraft kilns have burner ports on either side of the base of the kiln. The gas flames travel up the side of the kiln and heat up the chamber. Some gas kilns have something called a bag wall that sits between the flame and the pottery.
The bag wall is usually made of loosely stacked fire bricks that deflect the flame. This prevents the flames from touching and marking the ware. The bricks are positioned with gaps between them to allow heat to pass through the spaces into the chamber.
Whether the kiln has bag walls or not, the heat rises from the bottom to the top of the kiln. The chamber is heated en route. Updraft kilns have a flue on the roof of the kiln. The heat, along with fumes and gases that come from firing, passes out of the top of the kiln.
During firing a draft is being drawn in through the base of the kiln to the flue. Hence the name updraft. The volume of the draft can be controlled using a damper on top of the flue. If the damper is closed the flow of the draft is reduced.
Closing the damper reduces the amount of oxygen being drawn into the kiln. It also increases the amount of atmospheric pressure building up in the kiln.
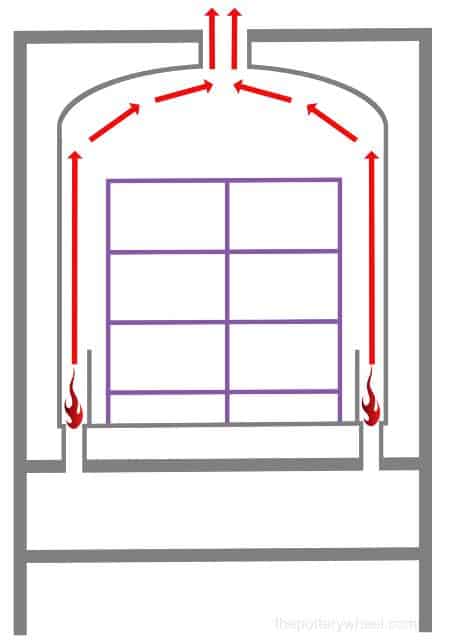
The amount of oxygen in the kiln will affect the look of the clay and glaze once it’s been fired. And the pressure building up in the kiln forces the heat to disperse into all areas of the kiln’s chamber.
So, adjusting the damper will change the way the pottery looks when unloaded. These processes are an important feature of the gas kiln, so it’s worth taking a closer look at them now….
Oxidation and Reduction
The amount of oxygen in the kiln determines whether the kiln is firing in oxidation or reduction. These terms can seem technical and off-putting, but they needn’t be. Here is a simple overview of oxidation and reduction:
During firing, fuel-burning kilns rely on the combustion of material to generate heat. Combustion requires oxygen to take place. If the kiln chamber contains plenty of oxygen the flame feeds of this supply.
However, if the oxygen supply in the kiln is limited, the flame looks for oxygen elsewhere. Both clay and glazes contain oxygen at a chemical level in the form of metal oxides. For example, iron oxide or copper oxide.
If the flame can’t find oxygen in the kiln atmosphere, it will draw it out of the clay and glaze. This alters the clay and glaze chemically by reducing the number of oxygen atoms they contain. This process is therefore called ‘reduction firing’ and the kiln is said to have a ‘reduction atmosphere’.
This chemical change will affect the color and texture of the ceramics. Glazes and clay that have been fired ‘in reduction’ will often have a more organic, rustic look.
By contrast, if the atmosphere is rich in oxygen, the flame will use that oxygen to burn. As a result, oxygen atoms are not stripped from the clay and glaze in the same way. When ceramics are fired in an oxygen-rich atmosphere, they are described as being fired in ‘oxidation’.
If the damper on a gas kiln is opened up, the draft flowing through the kiln draws in more oxygen. This creates an oxidation atmosphere.
By contrast, if the dampers are closed, the oxygen flow is reduced, and the kiln goes into reduction. So, gas kilns have the flexibility of working either in oxidation or reduction.
Downdraft kilns
Another gas kiln design is the downdraft kiln. Like the updraft kiln, heat enters the downdraft kiln at the base through gas burner ports. However, unlike the updraft kiln, the downdraft kiln does not have a flue at the top.
Because the heat has no way to escape out of the top, it is forced to circulate downwards again. The hot draft travels down into the kiln chamber and is effectively used to heat the ware twice. For this reason, downdraft kilns are considered to be more efficient than updraft kilns.
The flue on a downdraft kiln is at the base of the kiln. Once the draft has been forced downwards, it exits the kiln via the low-level flue into a chimney. The chimney carries away the heat, fumes, and gas from the kiln.
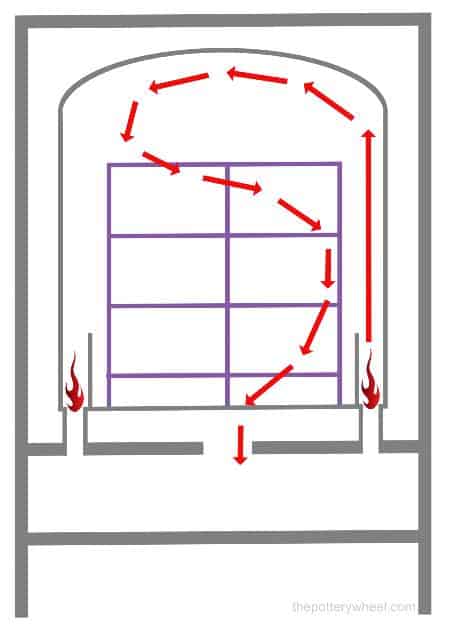
Like updraft kilns, downdraft gas kilns often have what is called a ‘sprung arch’ design. Sprung arch kilns have a curved arc ceiling that rests upon straight walls and a straight base. Iron angle is then used to support the walls of the kiln. Then the entire construction is encased in an iron jacket that supports and protects the chamber.
The shape of a sprung arch kiln looks a bit like the cross-section of a loaf of bread. The curved arch is achieved by using tapered bricks. And the degree of the curve will depend on how tapered the bricks are.
Most gas kilns are front-loading, which means that the door to the kiln is on the front. These doors can be hinged. But they can also be free-standing. If they are free-standing, they are wheeled into position and clamped onto the kiln when it fires.
2) Electric Kilns
Electric kilns are a more recent development in kiln construction. Despite being the new kid on the block, electric kilns have become very popular. They are especially popular amongst hobby potters and small-scale pottery and ceramics outfits.
The reason for their popularity is that they are convenient and relatively economical to install and run. Some electric kilns need to be wired directly into an electric supply. Other electric kilns can be plugged into a domestic electricity supply.
Like gas kilns, electric kilns have an internal chamber that is insulated with refractory brick. A refractory material can withstand high temperatures and has insulating properties.
However, heat in an electric kiln is generated by metal coils. These metal coils, or elements, are positioned in grooves that are cut into the brick wall. An electric current flows through the elements and the metal coils heat up.
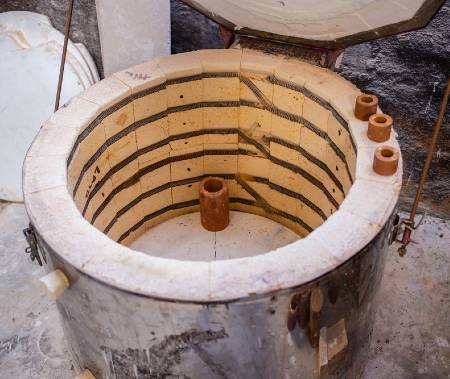
The elements are positioned around the side of the kiln because as they heat up they become soft. At 1800F (982C) the elements actually become floppy and can’t, therefore, be used on the ceiling of the kiln (source).
The types of kiln used for firing glass are designed to hit lower temperatures, below 1700F (926C). Therefore, glass firing kilns will have elements on the ceiling.
The heat then radiates around the kiln chamber. A lot of modern electric kilns are controlled by digital kiln controllers. These allow you to pre-program the kiln to ramp through a carefully controlled firing schedule. Once you have got the hang of the controller, you can program the kiln and leave it to ‘do its thing’.
Having said that, although you can program an electric kiln, all kilns need monitoring as they fire. It’s not safe to leave a kiln unattended as it fires.
Kiln Sitters
Other, older electric kilns rely on a ‘kiln sitter’ control. A kiln sitter is a partly mechanical device that uses a pyrometric cone. These are specially made ceramic bars that bend when they are heated up. Different cones bend at different temperatures.
As the kiln heats up the cone begins to bend. The kiln sitter is designed so that when the cone bends sufficiently, it switches the kiln off. Once the kiln has reached the desired temperature, the cone will have bent enough to trip the off switch.
Oxidation Firing
Because electric kilns do not burn fuel, they don’t need a supply of oxygen during firing. Oxygen is not being burned, so no through draft is required. Although oxygen is not being drawn into the kiln, it is not being used in combustion. Therefore, electric kilns operate in an ‘oxidation atmosphere’, which is rich in oxygen.
The chemical processes that clay and glaze go through in an oxidation or reduction firing are quite different. So, the difference in color and texture of pottery fired in these two atmospheres are striking. For example, if there is copper in a glaze it will turn red in reduction. However, the same glaze will turn green in an oxidation atmosphere.
The results of firing in an electric kiln are much more predictable and repeatable. And colored glazes fired in oxidation will tend to be brighter.
Ventilation
Electric kilns are neither updraft nor downdraft. However, they do need to be vented and some ventilation systems rely on creating a draft. During the firing process moisture, gases and fumes come off the heated ceramics. These need to be vented out of the kiln.
An electric kiln doesn’t have a flue as such. However, some have a hole with a bung on the lid for the purpose of venting. Others don’t have a hole in the lid, but they do have peepholes on the side. The peepholes or spy holes are partly used to let the potter see inside the kiln as it fires. But they are also used at times to allow for some ventilation to go on during firing.
A simple ventilation system is a cross draft arrangement. The kiln is positioned near an open window. And a fan is used to blow heat and fumes away from the kiln.
Other more efficient venting systems involve positioning a vent on or near to the kiln to draw the fumes away. Sometimes these systems draw the moisture and gases out of the bottom of the kiln. This is a downdraft venting system. Other vents are positioned over the kiln and draw the fumes and water away from the top of the kiln.
Electric Kiln Designs
Some electric kilns have a hinged door on the front of the kiln. These are called front-loading kilns. Other kilns have a hinged lid that opens upwards like a freezer cabinet. These are called top-loading kilns. Electric kilns can vary greatly in size and capacity. They range from a small countertop kiln to a large freezer sized kiln.
Another kiln design is the “top hat kiln”. With a top hat kiln, the ware is loaded onto a base or plinth. Then the heating chamber is lowered down on top of the plinth. Once the pottery has been fired and cooled the chamber is lifted off and the base can be unloaded. The chamber is usually lifted with a hand crank, that uses a system of pulleys that suspend the lid.
Top hat kilns can be used to bisque fire and glaze fire. However, they are also a popular choice for raku firing. So, let’s take a look at another type of kiln called a raku kiln.
3) Raku Kilns
Raku is a particular approach to firing, which involves removing the pottery from the kiln when it is red hot. The pottery is then put in a closed container of some kind, along with some combustible material like paper. The combustible material burns when it makes contact with the hot ware.
Because the fire is happening in a closed container, a reduction atmosphere is formed. This creates certain characteristic raku effects on the pottery glaze. The container can be as simple as an inverted steel bucket. Just as long as it can withstand the heat from the pottery and flames.
Making raku involves removing the pottery when the kiln is hot. As such electric kilns are not usually used for the raku firing process. The sudden drop in temperature when the kiln is opened can shorten the life of the electric elements.
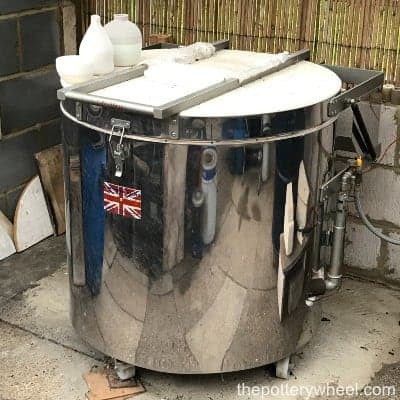
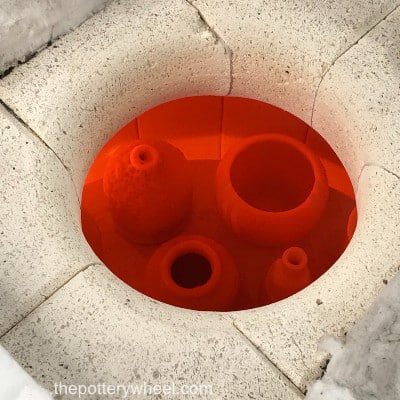
Mostly raku is made in gas-burning kilns. A common choice for raku is propane gas. Raku kilns come in all shapes and sizes. They can be commercially produced front loading or top loading gas kilns. Or they can be simply made DIY type raku kilns.
The top hat design is one of the more popular types of kiln used for raku. This is because when the hood is lifted the hot ware is easy to access and unload with tongs.
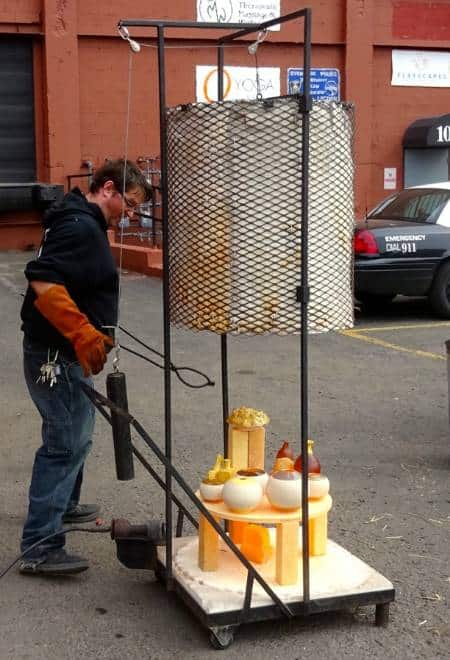
4) Car Kilns
Some types of kiln have a static base. With these kilns, the door is positioned on the base and locked in place. As described above, these moving doors can be front-loading, top-loading, or top hat in design.
An alternative design is that the chamber of the kiln is static, and the base of the kiln moves. These kilns are called car kilns because the base of the kiln moves. And the ware travels through the kiln on a car.
Some car kilns are huge industrial-sized kilns, known as tunnel kilns. These are continuous kilns that stay on and the ware is fired as it moves through the tunnel.
However not all car kilns are continuous, nor are they all massive industrial kilns. Some kilns that are used by smaller-scale potteries or schools also have a moving base.
The door to the kiln is attached to the car base. The ware is loaded onto the base, then the base slides into the kiln chamber. The door is then clamped in place and the kiln is switched on. These kilns are intermittent or periodic because they are allowed to cool before they are unloaded.
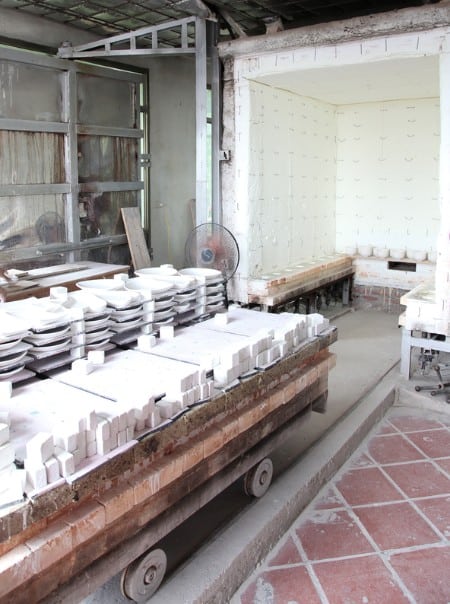
Another variation of the car kiln design is the shuttle kiln. Shuttle kilns have a door on either side. The car base slides in and out of the kiln. It can be loaded up at one end, travel through the kiln. It can then exit and be unloaded out of the other door. Hence the name ‘shuttle kiln’.
Traditional Types of Kiln
Each of the kilns outlined above is quite modern in its design and use. However, kilns have been used for thousands of years to make usable pottery. And many of the features of modern kilns are adapted from more traditional kilns. So, let’s have a look at some of these original kilns….
5) Climbing Kilns
Climbing kilns are large hillside kilns that were first built in China around 500AD (source). The kilns that originated in China were called Dragon kilns, and are the basis from which Japanese Anagama kilns evolved.
Climbing kilns were built along the upward slope of a hill and make use of the fact that heat rises. Some climbing kilns were simply a long tunnel that was not divided into chambers. These single-chamber kilns had shelves on either side of the kiln on which the ware was placed.
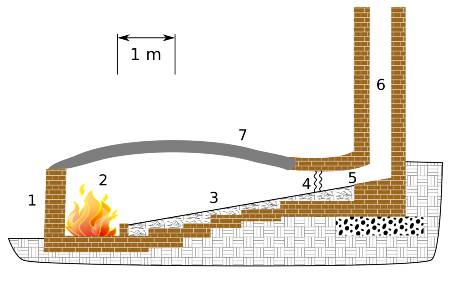
Via Wikimedia Commons
Other climbing kiln designs had multiple chambers. Heat would pass through one chamber and then enter the next chamber along. Some climbing kilns had a firebox beneath each chamber. Others had ports along the side of the kiln and fuel could be added that way. Most of these kilns were fueled by wood, but some were fueled by coal.
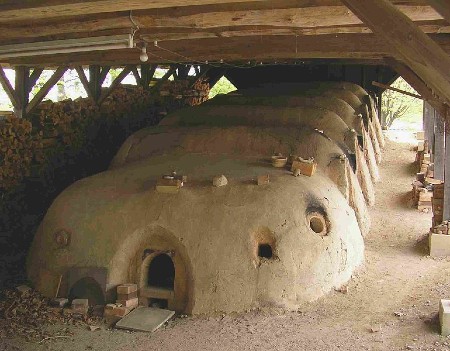
via Wikimedia Commons
6) Wood Burning Kilns
Although most of the large climbing kilns were wood burning, there are lots of different types of wood-burning kiln. They range from huge anagama kilns, to small igloo-shaped brick kilns built by individual potters in their back yard.
In spite of this range, there is a common type of construction used nowadays by potters who want to wood fire. Typically, wood-burning kilns today are built in the shape of a catenary arch. The sprung arch kiln, described above has an arched roof supported by straight walls. By contrast, the shape of a catenary arch kiln is one smooth curve from floor to ceiling.
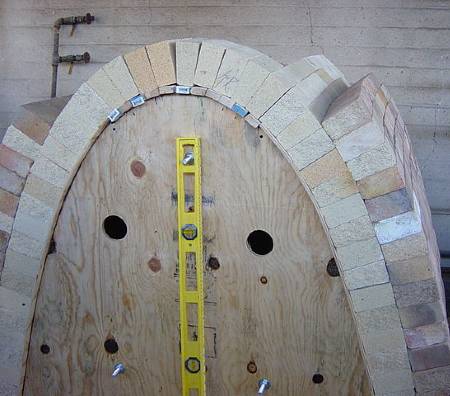
User:Leonard G., Public domain,
Via Wikimedia Commons
They are normally constructed by building the arch around a supporting arc-shaped structure. The bricks are then secured by cement and insulated on the outside. A common type of insulation is adobe, which is a primitive building material made from earth, straw, grass, and water.
Once the arch has been sealed and insulated it is self-supporting. At this point, the original supporting arc shape structure can be removed.
A wall is then built at either end of the arch to enclose the internal chamber. A chimney is built at one end of the arch. And an opening is left at the other end to feed wood into the kiln as it burns.
In simple designs, the fire is just positioned at one end of the kiln. However, sometimes a firebox is constructed to separate the fire off. Having the fire at one end and the chimney at the other creates an updraft flow.
Firing the Wood Burning Kiln
Using a wood burning kiln is a lot of work. The fire needs to be stoked continually to keep the temperature in the kiln high enough. Usually, this requires two or three people to be working in relay to keep the fire going. Often the kiln will be burning for around 72 hours.
Pottery that is fired in a wood burning kiln is often put into the kiln unglazed. This is because the hot ash from the burning wood settles on the pots and creates a natural glaze. Also, the effect flames that touch the pots directly can leave a beautiful, unpredictable finish.
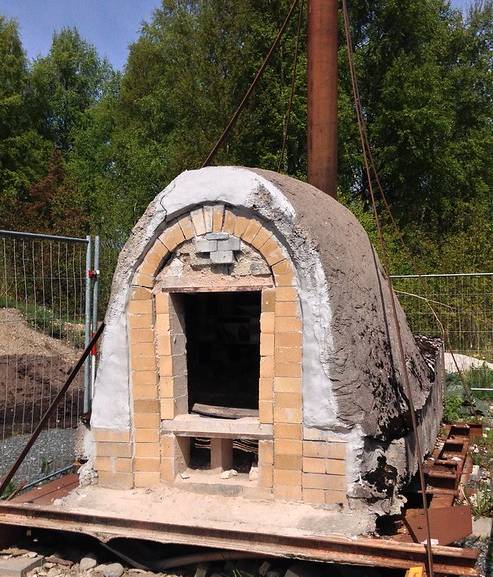
7) Soda Kilns
Like wood burning kilns, soda kilns are made from brick and are usually large enough to walk into. They are typically made with a sprung arch or catenary arch design with a chimney at one end. Soda kilns are often fueled using natural gas, though sometimes they are wood fired.
Whilst pottery is being fired, a sodium solution is sprayed into the kiln. It is often sprayed into the kiln when the kiln has reached around 2336F (1280C). This is cone 9 temperature, so soda firing is suitable for firing stoneware.
The solution is made by dissolving sodium bicarbonate into water. This vaporizes, coats the pottery, and reacts with the clay to form a glaze.
The glaze often has a dimpled orange peel texture. And is characterized by changes in color and tone where the sodium solution has hit the pots. This is known as a flashing effect.
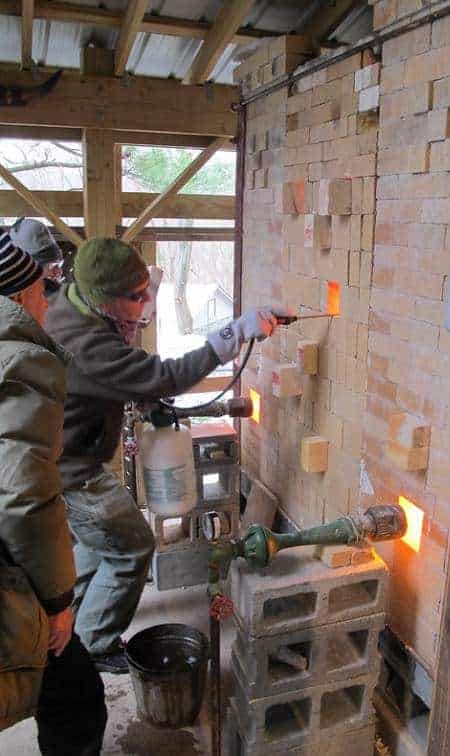
(CC BY 2.0)
Often soda kilns don’t have a door. Instead, the kiln is bricked up at the entrance each time it’s fired. The sodium solution is sprayed through a hole in the door where a brick has been removed. Once the kiln has cooled, which normally takes a couple of days, the ‘door’ is removed brick by brick.
8) Beehive Kilns
One of the earliest types of kiln to be used is the Beehive kiln. These are large brick constructions used for industrial-scale production of pottery.
Beehive kilns are squat circular kilns with straight walls and a domed roof. They do, indeed look a little like the top half of a beehive. Beehive kilns could be downdraft or updraft. Almost all beehive kilns are no longer in use.
However, there are a small number of exceptions to that. One exception being the downdraft beehive kiln at Errington Reay Pottery in Northumberland UK. This kiln produces salt glazed pottery and is fueled with coal. (Source)
Large Beehive kilns tended to be downdraft in design and had a chimney. These kilns were heated by adding fuel to a firebox at the side of the kiln. The heat then entered the kiln and was directed upwards by a bag wall. When the heat reached the closed ceiling, it is forced to circulate downwards again.
The heat and fumes then leave the kiln through a flue in the floor. It travels underground through the flue until it reaches a chimney that is situated separately from the kiln.
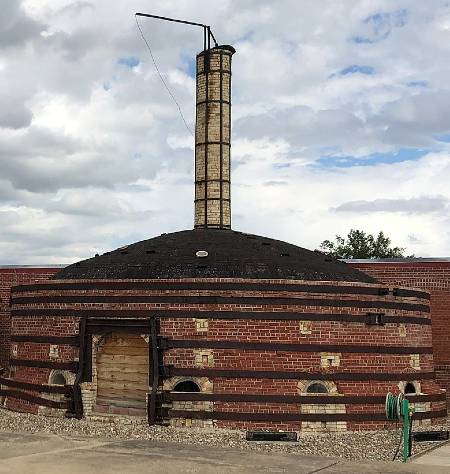
Other simple beehive kilns have a straightforward updraft design. In these kilns, the heat rises through the kiln and exits a short flue on the top of the kiln. These kilns are similar in design to another early kiln design called the bottle kiln.
Because of their similarity, the terms beehive and bottle kiln are sometimes taken to mean the same thing. However, there are some differences, so let’s take a look at bottle kilns now….
9) Bottle Kilns
Bottle kilns were developed later than beehive kilns and have a different shape. As their name suggests, bottle kilns are tall bottle-shaped constructions. Like beehive kilns, they are traditionally used for industrial-scale production. They fired large quantities of ware at a time and a factory aimed to fire the kiln once a week.
However, bottle kilns are intermittent, meaning they are fired, cooled, and unloaded. Because most industry relies on tunnel/car continuous kilns these days, bottle kilns are increasingly a historic curiosity.
Another reason that bottle kilns have fallen out of favor is that they were usually fueled by coal. And coal has been a significant contributor to air pollution.
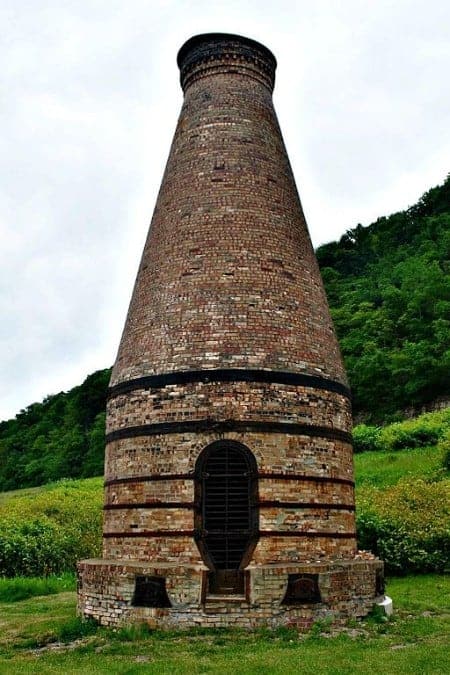
There is a distinction between bottle ovens and bottle kilns. Bottle ovens were used to bisque and glaze fire ware. Whereas bottle kilns were either Muffle Kilns or Calcining Kilns.
Muffle kilns were bottle kilns that were fired to a lower temperature. They were used to enamel pottery or fire decorative designs onto pottery that had already been glazed. Calcining kilns were used to fire ingredients that would be ground up like grog, and added to a clay body.
Bottle ovens have a flue on top, so it would be reasonable to think they had an updraft design. Whilst some are updraft, others had an internal chamber that was constructed with a downdraft flow.
Primitive Types of Kiln
In this section, I will look at two primitive types of kiln; pit firing and sawdust kilns. Pit fires and sawdust kilns are both sometimes made out of metal barrels, which is hardly a primitive material.
However, the original pit firing technique dates back to 800AD, and modern-day pit firing and sawdust kilns rely on these original principles. Pit firing is still a popular low-tech way of firing clay, as are sawdust kilns.
10) Pit Firing
One of the earliest, primitive types of kiln is pit firing. Pit firing involves placing ware in a pit in the ground along with combustible material. Some of the fuel that has been traditionally used is wood, straw, and manure.
The pit is lined with combustible material, and the ware is placed on top of this. It is then covered with more material and once it is completely covered, the fire is set alight. The fire is left to burn until the combustible material has been consumed by the flames. It is then left to cool and the ware is removed, cleaned, and often polished.
Pit firing doesn’t use a kiln in the usual sense of the word. However, it does use the same principles of kiln firing.
Basically, kilns are an insulated heating chamber. Whilst pit fires are dug rather than built, the walls of the pit create a chamber. And this chamber is insulated by the ground, not unlike an insulated kiln.
In addition to this, pit firing uses fuel, like other fuel burning kilns. However, unlike most kilns, with a pit fire, the fuel is placed on top of the kiln. And the insulating walls of the pit are underneath the fire. As a result, a lot of heat is lost from the pit as it radiates upwards. For this reason, pit firing is not the most efficient way of firing pottery.
However, heat in a pit fire can be contained. Once the fire is well established, the pit can be partly covered with sand or manure. This contains the heat and helps to create a reduction atmosphere.
One way of adapting this approach is to use a barrel as an alternative to a pit in the ground. This is known as a barrel kiln.
11) Sawdust kiln
The principle behind a sawdust kiln is similar to pit firing. Like pit firing, the ceramic ware to be fired is buried in the combustible fuel, which is sawdust.
As with each of the types of kiln described above, sawdust kilns vary in their construction. However, a lot of sawdust kilns are built from brick. Their design can be very simple and can consist of a layer of builder’s brick for the base. With brick walls to construct a four sides simple box-shaped kiln.
A layer of sawdust is placed on the base of the kiln and the pieces are positioned on that layer. These are then covered with more sawdust, which is packed between the pottery. More layers of pottery can then be positioned on top of the first layer that is buried in sawdust.
A simple shelf can be used to separate out the layers of pottery. This shelf can consist of a metal grid that is held in place by being sandwiched between the wall bricks.
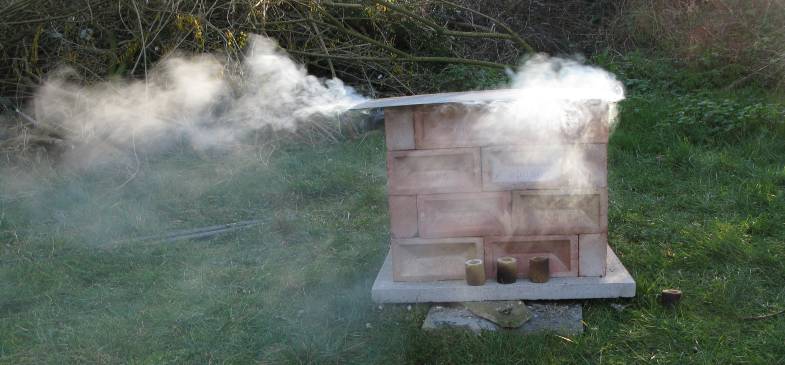
Once the brick box is packed out with sawdust and pottery, the sawdust is set alight. Once the fire is established, the top of the kiln can be covered with a fire-resistant lid. The atmosphere in the kiln can be adjusted by making a gap between the lid and the walls. There needs to be some gaps in the wall of the kiln too, to allow for some oxygen.
The kiln is allowed to fire until all the sawdust has burned away. As with pit firing, an alternative sawdust kiln construction is to use a metal barrel.
Final Thoughts
There are many types of kiln that have been used over the years, and that are currently available to potters. These kilns are so different that it’s almost a stretch to use the word ‘kiln’ to refer to them all. For example, consider the difference between a simple sawdust ‘kiln’ and a mass-production continuous kiln. Nevertheless, although they are vastly different, they share an end goal of firing clay. With so many types of kilns available, you are bound to find a method of firing that suits you.