Your cart is currently empty!
What is Pottery Glaze Made of? Understanding Pottery Glaze
Published:
Last Updated:
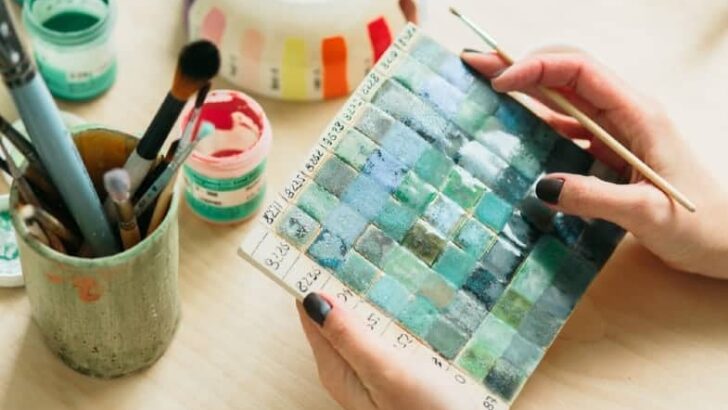
Affiliate Disclaimer
As an affiliate, we may earn a commission from qualifying purchases. We get commissions for purchases made through links on this website from Amazon and other third parties.
Glaze is the glass coating on the surface of pottery items. It can give the surface a glossy, matte, smooth, textured, opaque, or clear finish. Varying glaze compositions result in different glaze outcomes after firing. Each component has its function that like magic, transforms the glaze’s appearance after firing.
Pottery glazes consist of three basic components. The basic components are: Firstly, glass-forming substances (silica or boron trioxide). Secondly, a refractory or stiffening component (alumina). Lastly, a flux component. Other additives are mixed with these basic components. They provide the color, determine glaze opacity and create other desired finishes.
Ceramic glaze refers to a vitreous substance fused onto pottery through firing. Glaze has three basic functions. Firstly, glaze seals the inherent porosity of earthenware vessels rendering the vessels suitable for holding liquids. Also, glaze gives ceramics a tougher surface. Finally, glazes enhance the underlying texture or design painted, carved, inscribed, or unmodified.
Together, the basic components and the additives undergo chemical reactions during firing that change their appearance like magic.
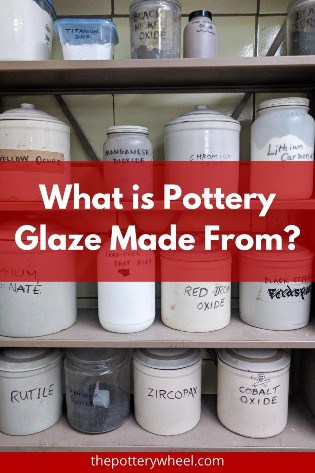
What is Pottery Glaze Made of?
The Basic Components
The basic components are found in varying formulations in almost all glazes. The additives are selected according to the desired glaze finish after firing. Here is a closer look at the basic components of pottery glaze…
1) Glass Formers
The glass-making component changes the glaze into a glassy substance that coats the pottery surface. The most common glass former is silicon dioxide or silica. Silicon dioxide can be found in quartz, flint, and other metal oxides.
When silica is heated in the kiln to a temperature of over 3100 degrees Fahrenheit, it melts and turns into glass. However, the melting point of silica is too high and cannot be obtained by any ceramic kiln. As a consequence, silica cannot be used on its own as a glaze. Also, too much silica will slow down or inhibit the melting of glaze or produce an uneven surface.
2) The Stiffener or Refractory
Aluminum oxide is used as a stiffening or stabilizing agent which prevents the molten glaze from running off the pottery surface. The stiffener helps the glaze stay in place while the pottery is in a vertical position.
Alumina is also called a refractory because it helps the glaze withstand the firing temperature without sliding off the pottery. In addition to stiffening the glaze, alumina also helps in dispersing fine gas bubbles that form when silica is heated till it melts.
Finally, alumina has a pink coloration and is thus used in coloring the final piece. Alumina as calcined alumina or alumina trihydrate can be found in clay, cryolite, and feldspars. Alumina also helps disperse gas bubbles on the glaze surface.
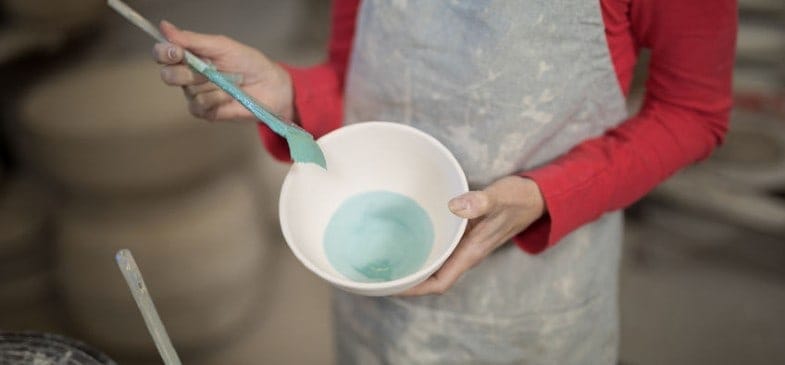
3) Flux
As mentioned earlier, the melting temperature of silica at approximately 3100 F (1710 C) is higher than the heat in any ceramic kiln. For this reason, flux is added to the glaze mixture to lower the melting temperature of mineral compounds like silicon dioxide in pottery glazes.
It is important to note that fluxes act as impurities lowering the melting point of silica. Some examples of fluxes used in glaze are bone ash, and oxides of potassium, sodium, calcium, and zinc.
Fluxes are chosen depending on the firing temperature range of the glaze. For example, fluxes that are very active allow the glaze to mature at earthenware temperature. As a result, they are used in kilns with low firing temperature ranges.
On the contrary, less active fluxes are used only when the kiln requires mid-to-high range temperatures. In this regard, it is important to find out the nature of a particular flux before using it in your kiln.
Also, fluxes such as oxides of sodium, potassium, and calcium are toxic and must be handled with care. For instance, ensure you wear a dust mask when handling these fluxes. At the same time, you should ensure that your final cup, plate, or bowl reaches full maturity to prevent any flux from leaching into food or water served in or on it.
Balancing the Three Basic Ingredients of Glaze
As highlighted in the previous section, each of the three basic components performs a specific function. In this regard, it is essential to a have balance of silica, alumina, and flux in your glaze to ensure that you don’t run into problems during glazing.
More importantly, care must be taken to ensure that none of these components is in excess due to the potential adverse effects of having too much of the ingredients.
In the first place, too much silica inhibits the melting of glaze resulting in a roughly textured surface. Silica that has not become molten can form crystals producing harsh dry surfaces in the final finish.
Further to this, too much alumina stiffens the glaze leading to a poor quality finish. And too much flux causes glaze to run creating variable texture on the surface of the glazed ceramic. Specifically, the texture may be shiny where glass is balanced, but rough where there is excessive flux.
What is Pottery Glaze Made of? The Additives
A glaze may include one or more of the following additives depending on the intended surface finish:
1) Colorants
Molten silica is transparent. That’s why it is necessary to add colorants to achieve the desired glaze colors after firing. It’s important that the colorant used can withstand the intended firing temperature. Some colors lose their intensity or hue when fired at higher temperatures.
The common colorants used for glaze are copper carbonate, copper oxide, iron oxide, chromium oxide, and cobalt oxide. Talc is used as a whitening agent.
Raw metal oxides and carbonates usually produce a different color after glaze firing. It is important to know the colors each metal oxide will become after firing. Some colorants are used less often. These include antimony to produce yellow, cadmium, and selenium for bright red and gold for pink, purple, and red.
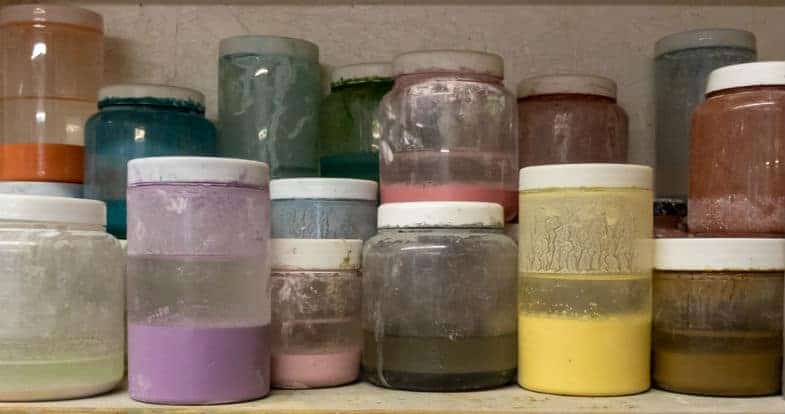
2) Suspending Agents
Suspenders keep the heavier components of the glaze suspended and prevent them from settling at the bottom of the container. Some of the commonly-used suspenders are bentonite, ball clay, china clay, and kaolin.
3) Opacifiers
Opacifiers are added to glazes that should have an opaque or white background. Some of the commonly used opacifiers are tin oxide, zirconium, titanium, zinc, and bone ash. Opacifiers are usually used together with colorants to produce an opaque, colored glaze.
4) Gums
Gums are added so that the glaze will harden once it has been applied and before it has been fired. Adding gum to the glaze makes the handling of the pottery safer.
Gums also improve the adherence of the glaze to the pottery surface. It also slows down glaze drying for easy brushing as well as reduces shrinkage.
Some of the commonly-used gums are Gum Arabic, and sodium carboxymethylcellulose (CMC Gum).
5) Glaze Thinners
In some instances, the final finish is too thick for use. In such a case, sodium hexametaphosphate in water is used to thin a glaze that has too thick a consistency. Furthermore, glaze thinners enable a glaze to be thinned for spraying.
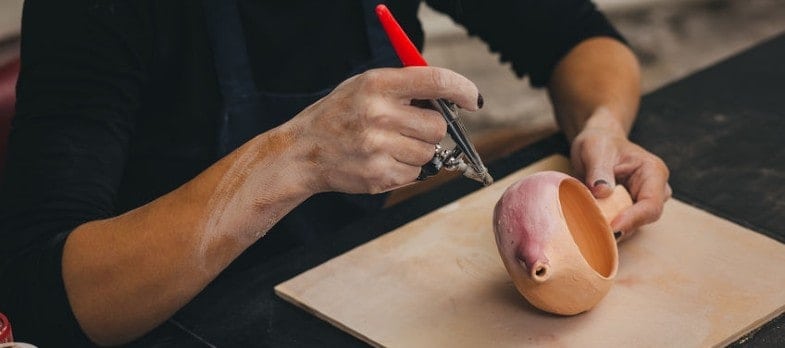
Final Thoughts
A basic understanding of what pottery glaze is made of yields consistent and desirable results, as each of the basic components of glaze has its own function.
Becoming familiar with what your glaze is made of will make the process of glazing easier. You can avoid glazing problems or deal with them more efficiently when they arise. It would also be easier to adjust or troubleshoot your glaze problems because you know the composition.