Your cart is currently empty!
Does Underglaze Stick to the Kiln Shelf?
Published:
Last Updated:
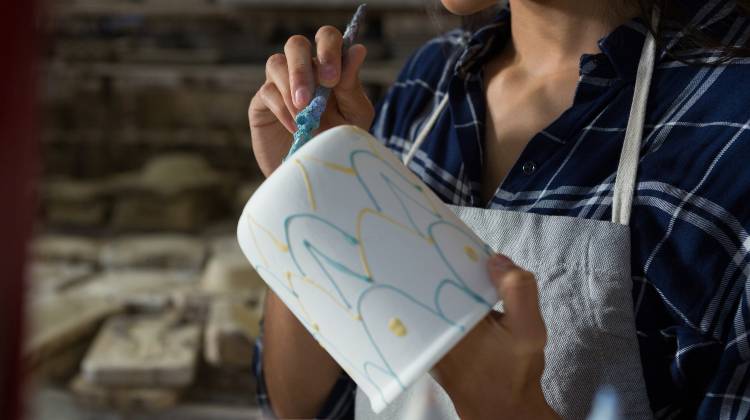
Affiliate Disclaimer
As an affiliate, we may earn a commission from qualifying purchases. We get commissions for purchases made through links on this website from Amazon and other third parties.
Pottery glaze melts when it is fired and will stick to the kiln shelf if it isn’t wiped off. But what about underglaze? Can you put it on the bottom of your pots, or does underglaze stick to the kiln shelf?
Many types of underglaze don’t stick to the kiln shelf when they are fired. However, some underglazes will melt a little and stick to the kiln or other pieces of pottery. It depends mainly on the brand of underglaze and the temperature that you are firing at.
Why Does Underglaze Sometimes Stick to the Kiln Shelf?
There are a few factors that affect whether your underglaze will become sticky when it’s being fired. Here is a closer look at some things to consider…
1) The Underglaze Ingredients
Underglaze is made of colored ceramic stains that have been mixed up with water, clay and a suspending agent like CMC gum. The suspending agent keeps the powdered stain mixed up with the liquid rather than separating completely when the underglaze is left to settle.
However, some underglaze also contains silica which melts when it is fired in a kiln. Silica is one of the glass-forming ingredients in pottery glaze that melts and gives glaze its glassy quality. Silica can be derived from the mineral quartz.
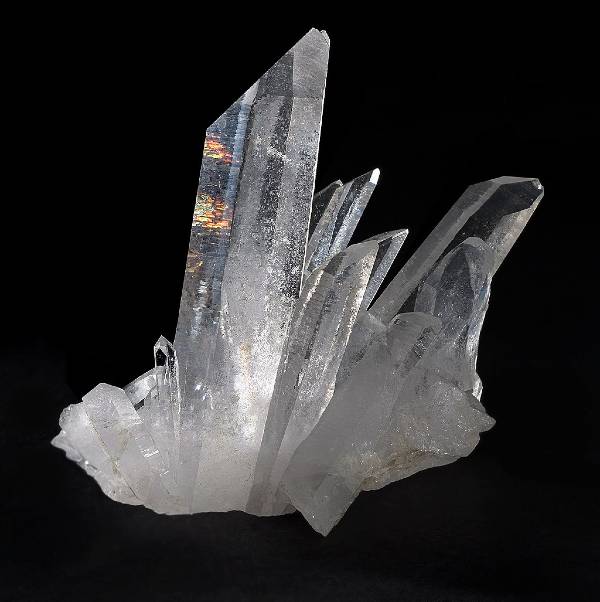
The difference between glaze and underglaze is that if the underglaze does contain silica, it contains much less than a pottery glaze. So, whilst the silica may give the underglaze a slightly glossy sheen when it’s fired, it doesn’t melt as much.
Nevertheless, when underglazes contain glass-forming ingredients, they can melt a bit when they are fired. This is one of the reasons why underglaze can sometimes stick to the kiln shelf.
It is also why different pieces of pottery that have been decorated with underglaze can also stick to each other when they are fired. For example, if you put underglaze on the rim and gallery of a lidded pot, the two pieces may fuse together when they are fired.
Ceramics manufacturers don’t normally state what ingredients they have used to make their products, so it can be hard to tell without using an underglaze what it will be like when it’s fired.
If you want to know, you could email the manufacturer and ask them if their underglaze is likely to flux (melt) when it is fired. I’ve found that ceramics manufacturers are normally responsive and helpful with these kinds of queries.
2) The Brand of Underglaze
Different brands of underglaze have different properties. For example, some underglazes are completely matt, whereas other brands can have a slight satin sheen on them when they are fired.
That’s because they are made of different ingredients. Some brands of underglaze contain more silica than others. For example, Duncan Concepts underglazes have a glossy sheen when 3 coats have been applied and they have been fired.
I like Duncan Concepts underglaze, but they are known for being adhesive when they are fired.
3) The Color of the Underglaze
Another factor that can affect if the underglaze will stick to the kiln shelf, is the color of the underglaze. Generally, darker colors are at a higher risk of sticking than lighter colors.
The reason for this is that darker ceramic stains like cobalt and black are more likely to flux at higher temperatures when they are fired.
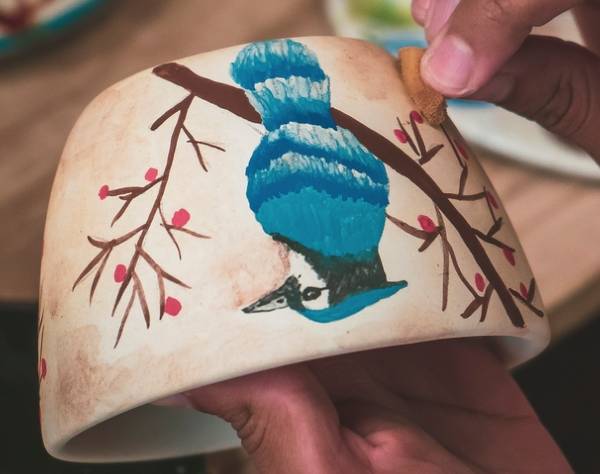
4) The Firing Temperature
Whether the underglaze will stick to the kiln shelf or not also depends on the temperature that you are firing at. This is because underglaze and glaze ingredients melt at different temperatures.
The underglaze may not melt and stick at bisque temperatures of around 1832F (1000C). However, at higher mid or high-fire temperatures around 2228F (1220C) and above, the same underglaze may start to melt.
So, if you are firing and glazing your pots in the lower earthenware temperature ranges, you might be ok and your underglaze may not stick. But if you are firing at mid to higher temperatures then your underglaze might be more at risk of fluxing.
5) The Thickness of the Underglaze
Underglaze is applied in layers. You can build up a deeper color if you apply 3 layers to your piece. However, the thicker the application, the greater the chance that the underglaze will stick to your kiln shelf.
A Combination of Factors
Sometimes your underglaze will stick because of a combination or mixture of the above factors. Some lucky potters can happily underglaze the base of their pottery and never encounter any issues with sticking.
However, if you are trying out a new underglaze, and you want to use it on the base of your pots, sticking is a risk. So here are some measures you can take to avoid losing your work or damaging your kiln shelves.
How to Prevent Underglaze Sticking to the Kiln Shelf
Tip 1 – Test the Underglaze
If you are using a new underglaze it’s best to try testing it out first before you apply it to your finished greenware. Paint some underglaze on a piece of scrap clay and then put it on a kiln cookie.
A kiln cookie is a small thin patty of clay that you can use underneath your pots when you fire them to catch any glaze drips. You can read more about how to make and use kiln cookies here.
Try firing the test piece at the temperature at which you want to fire your greenware. If the underglaze sticks to the kiln cookie then it’s likely that it would stick to the kiln shelf too.
Tip 2 – Add a Foot Ring
If you put a foot ring on your piece, you can underglaze the recessed part of the base. That way you get the color and decoration on the base, but the foot ring that is in contact with the kiln shelf is raw.
Tip 3 – Using Kiln Stilts
Kiln stilts are small prongs that your pottery can rest on when it’s being fired. They are often triangular and can be made from bits of wire supported in a piece of ceramic material. Alternatively, they can be made of high-fire ceramics without the metal.
Kiln stilts raise your pottery off the base of the kiln so that the base isn’t in contact with the shelf as it fires. The benefit of stilts is that you can decorate the base of your pot. They leave only a small mark on the base where the point of the stilt has been in contact with the base.
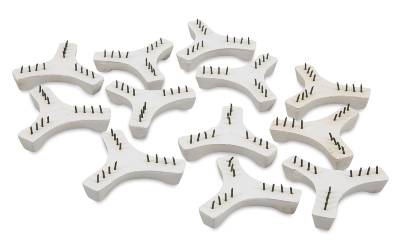
However, stilts with metal prongs will bend at higher temperatures (source). This can cause your pots to topple over in the kiln if they are fired at stoneware temperatures.
Also, I’ve found it’s best to avoid using stilts with larger flatter pieces like plates and platters. If a large flat piece of clay is only supported at a few points when it’s being fired, the clay can warp in the kiln.
As a result, you can be left with a bent misshapen plate, especially if you are firing at mid to high-fire temperatures when the clay will become soft during the firing.
Tip 4 – Wadding
Another alternative to using stilts in your kiln is to make some wadding to support your pots. Wadding is a refractory material that can be rolled into small buttons. The word refractory means that it has a melting point that is much higher than a kiln could reach.
These buttons can be pressed onto the bottom of your pots and will lift the pot just off the kiln shelf. They will stick to the bottom of the pot a little during firing. However, they can be knocked or chiseled off the base easily once the pot has been fired.
Ingredients for a simple wadding recipe:
- 50 % alumina hydrate
- 50% kaolin/china clay
These powders are mixed with water and combined to make a clay-like mixture. Small blobs are then put on the bottom of bisque pots before they are fired.
What to do if Underglaze Sticks to the Kiln Shelf
If underglaze does stick to the kiln shelf, it’s normally much easier to remove than pottery glaze. Your pots won’t weld as firmly to the kiln, particularly if you have used kiln wash.
Usually, you can dust or lightly sand the kiln wash off the base of the pot. The problem with sanding is that the underglaze will come away with any kiln wash or debris that’s attached to the base.
I have found that items sticking together with underglaze are more problematic. This is particularly the case with tightly fitting items. For example, I have used underglaze on the inside surface of lids and found that they bond to the gallery of the pot.
When this happens, you can try various ways of getting the lid off the pot, such as tapping it lightly or running it under warm water. Sometimes the lid will shift, but on the occasions this has happened to me, the lid has remained stuck in place.
Alternatives to Using Underglaze on the Bottom of Pots
Underglaze is not the only way of adding color or decoration to your pots. Here are a couple of suggested alternatives:
1) Colored Decorating Slip
Decorating slip is clay slip that contains ceramic stains. Because clay is the main ingredient in decorating slip, you don’t need to worry that it’s going to melt onto your kiln shelf or bond your pottery together.
What’s more, I find that colored slip gives pottery a buttery-rich finish that can sometimes be missing with underglaze.
2) Colored clay
Another alternative is to add color to the clay body itself. There are a few ways of making colored clay. It’s quite a simple process and you can read more about how can be done here.
When you are using colored clay, you don’t need to worry about adding colored decoration to the base, because the clay itself is the decoration.
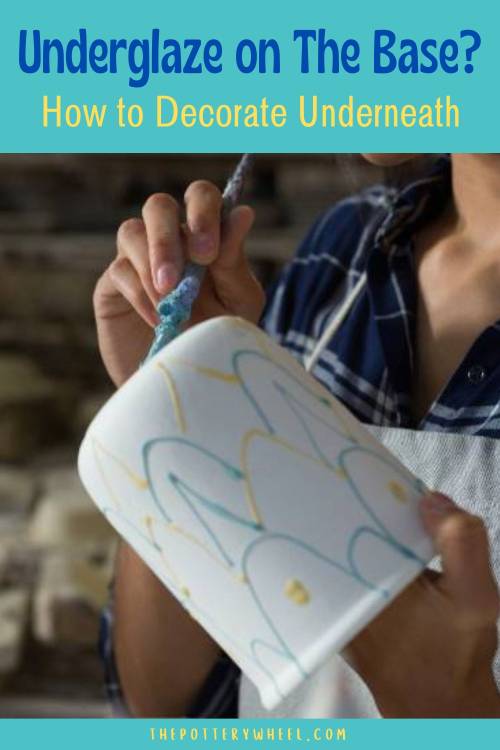
Final Thoughts
Whether your underglaze will stick to your kiln shelf depends on a few factors. I think the best suggestion is to test out the underglaze first before committing it to your finished pottery. Doing a test fire on a small sample piece can feel like a boring delay if you are itching to get going on your work. But in the long run it will save you lots of hard work and heartache.