Your cart is currently empty!
Stoneware Vs Earthenware – How Do They Differ?
Published:
Last Updated:
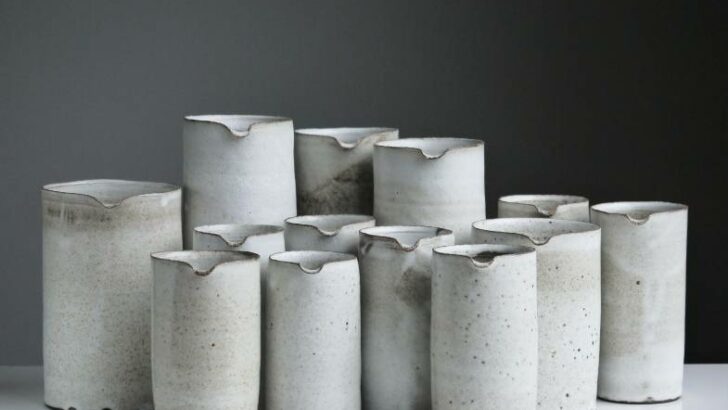
Affiliate Disclaimer
As an affiliate, we may earn a commission from qualifying purchases. We get commissions for purchases made through links on this website from Amazon and other third parties.
In the field of pottery, there are lots of different types of ceramic ware. Very broadly, ‘ware’ is a term used to refer to pottery objects, in their different stages of being made. You may have wondered what the difference is between stoneware and earthenware. This article will compare stoneware vs earthenware, and in particular, we will look at the following:
- Stoneware vs earthenware ceramics
- Stoneware vs earthenware clay
- How stoneware and earthenware ceramics are made
- Which is best for ovenware or dinnerware

The production of pottery involves turning soft, soluble clay into hard insoluble ceramics. First, the soft workable clay is molded into the required shape. The clay is then dried out and then fired in a kiln. A kiln is basically an extremely hot oven.
The temperatures reaching in a kiln are much hotter than a domestic oven. And in the heat of the kiln, the clay goes through chemical and physical changes to become ceramic.
Ceramic is a broad term that refers to clay once it has undergone an irreversible change into something hard and insoluble. But different types of ceramic have different qualities. So let’s dive in and take a look at stoneware vs earthenware.
1) Stoneware Vs Earthenware Ceramics – The Differences
Stoneware and earthenware ceramics have different properties. So, let’s start off by looking at these two types of ware once they have been made into a piece of ceramic.
Earthenware Ceramics
When clay is fired, it becomes insoluble, which means that if it’s put in water, it won’t dissolve. However, even though it does not dissolve, ceramic ware is more or less porous. Whilst fired clay won’t dissolve, some types of clay will still absorb water because it is porous.
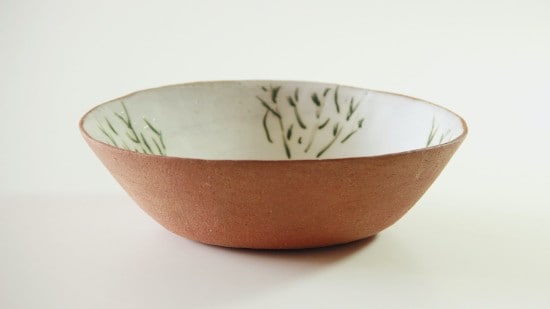
Porosity
Compared to stoneware, earthenware ceramics are relatively porous. In fact, some sources define earthenware ceramics as a fired body with more than 5% porosity (Hamer & Hamer, 2015, p123). Porosity is the percentage of void or pore space in the ceramic ware.
Whilst 5% does not sound like much, if you dunk earthenware in water, it will soak up water like a sponge. Because earthenware is porous it needs to be coated in pottery glaze to be watertight.
Firing clay is normally done in two stages. The first stage is the bisque fire, where the clay is transformed into ceramic ware. The fired pottery, called bisque ware, is then coated in a liquid glaze. This is essentially ground-up glass powder suspended in water, mixed with some other ingredients.
The second fire is the glaze fire. During the second fire, the glaze powder melts into a liquid glass, which covers the pottery surface. When the kiln cools the glaze becomes a solid glassy layer on top of the pottery.
This glassy layer makes earthenware waterproof. As such it can be used to make liquid holding items like vases, cups, and dinnerware.
Strength
Though earthenware can be made watertight through glazing, it is not particularly strong. Because earthenware is porous, it is relatively weak and will chip and break quite easily. As a result, functional items made from earthenware tend to have a thicker cross-section than stoneware items which are stronger.
So, earthenware ceramics are often a bit thicker and chunkier than stoneware. In spite of this, they are still vulnerable to chipping and breaking. In fact, with some earthenware, you can mark it quite easily with your fingernail or a sharp piece of metal.
Stoneware Ceramics
As the name suggests, stoneware is an altogether tougher ceramic material than earthenware.
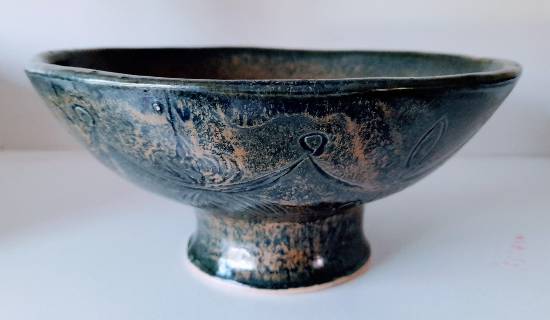
Porosity
Part of the reason for the strength of stoneware ceramics is that it is less porous than earthenware.
Exactly how porous a ceramic needs to be to be classified as stoneware varies between sources. For example, Hamer and Hamer, state that stoneware is a ceramic material that has a porosity of less than 5%. However, they go on to say that ideally, it should have an absorbency of 1 or possibly 2%. Whereas, other sources, state that the porosity of stoneware should be below 3%.
However, what is agreed is that stoneware pottery is sufficiently non-porous that it does not need to be glazed. When stoneware clay is fired correctly, it will not absorb or leak water once it has been made ceramic. As such, it can be used as functional ware without having a glassy layer coating.
Strength
One of the differences between stoneware and earthenware is the temperatures at which they are fired. I will say more about firing temperatures later. However, for now, it’s worth mentioning that stoneware is fired at a higher temperature than earthenware. Earthenware is normally fired at a temperature below 2109F (1154C). And stoneware is normally fired at temperatures above 2192F (1200C).
Because stoneware clay is fired at higher temperatures than earthenware, it undergoes more physical and chemical changes. And these changes make the stoneware pottery stronger. As such it is less likely to chip and or break when it is being handled and used.
Lots of different styles and types of ceramic can be called stoneware and earthenware. For example, slipware, maiolica, majolica, faience, and creamware are all types of earthenware. A beautiful example of tin-glazed earthenware is the Delft pottery of the Netherlands.
Likewise, there are different types of stoneware ceramics, ranging from salt-glazed ware to red stoneware and everything in between.
These differences are due to the types of clay used, different firing methods, and different ways of decorating the ware.
Let’s look first at the difference between stoneware and earthenware clay.
2) Stoneware Vs Earthenware Clay
A clay body can be produced in a few different ways. One way of producing clay is to mine it from the ground and then process it. Processing involves refining the clay and adding ingredients so that it’s suitable to be made into ceramic ware.
Alternatively, some clay is made by mixing powdered ingredients together. Some of these powdered ingredients were originally mined from the ground, processed, and then milled into a powdered form. An example of this is ball clay.
Clay is produced by the earth over thousands of years. Natural rock that is exposed to the weather is gradually eroded. As the rock is worn away, mineral deposits are formed out of the eroded rock particles. It is these mineral deposits that form the basic ingredients of pottery clay.
The mineral deposits can collect at the point of erosion. This is called primary clay and is how pure types of clay like kaolin are formed. Kaolin is the main ingredient of porcelain clay, which is known for its refinement and purity.
Alternatively, the sediment can be carried by water and wind and collect at another location. This is known as secondary clay.
On its journey, secondary clay picks up other impurities. Both earthenware and stoneware are secondary clays.
Earthenware Clay
Earthenware clay is made up of fine particles. This is partly because it is a secondary clay and has been transported from its original point of erosion. On its journey, the clay particles are broken down into smaller pieces. Having small fine particles makes earthenware clay quite smooth to handle. It also gives the clay a quality called ‘plasticity’. Clay with plasticity is easy to stretch, shape, and mold.
Earthenware clay comes in a range of colors including buff, brown, white, and grey. However, perhaps the most well-known earthenware clay is terracotta clay, which is typically a rich rusty red color. Red earthenware clay gets its distinctive color because it has a high iron oxide content. Terracotta clay is typically made up of 5% of iron oxide (source). Terracotta picks up iron as the clay sediment travels from its point of erosion to its final location.
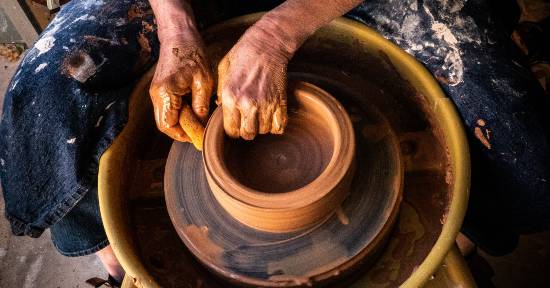
Iron melts (or fluxes) at relatively low temperatures. This is one reason why earthenware clays are fired at lower temperatures. Because earthenware clays contain impurities, they will start to bloat and warp at higher temperatures.
Stoneware Clay
Stoneware clay is often made up of lots of different-sized particles. These particles can include ball clay, fire clay, sand, and grog.
Grog is clay that has been fired into ceramic material and then ground up again into granules. Adding either grog or sand to clay makes it more workable. It does this by giving the clay a bit of internal structure or strength.
Very soft plastic clay can become a bit floppy and overly soft. Grog or sand gives the clay a bit of internal support and stops it from slumping when it’s being shaped.
Stoneware clay is often grey, buff, or off-white. When it is moist it is usually a darker grey. And when it is fired the color will lighten up. For example, a grey or buff clay will become a creamy white color when fired.
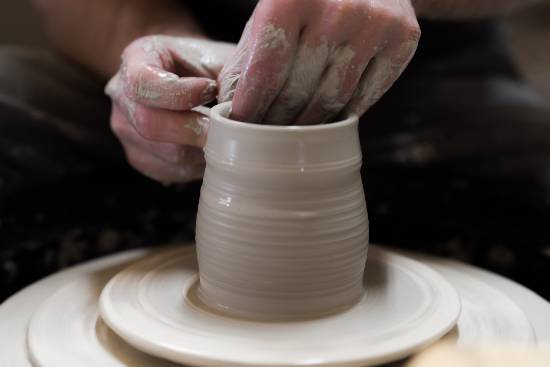
However, stoneware clay can come in a range of colors including red stoneware. Like terracotta red stoneware gets its coloring from its iron oxide content. However, red stoneware can be fired at higher stoneware temperatures.
Because of its iron content, red stoneware has to be fired carefully. Typically, organic and inorganic carbons are burned out of the clay during the first or bisque firing. It’s especially important that the burn out process is complete with red stoneware.
Problems can occur in the glaze fire if carbons remain in the bisque-fired pottery. During the glaze fire, the remaining carbons will take oxygen from the iron oxide in the clay. This turns the iron oxide into black iron oxide, which causes black coring. Black coring is when the clay turns grey or black under the surface layer.
This highlights the importance of how ceramics are fired. And this is what we come to in our next section….
3) How are Stoneware and Earthenware Ceramics Made
On the whole stoneware and earthenware clay can both be used for different pottery techniques. The main methods of making pottery are using a pottery wheel, hand-building pottery, and slip casting. If you’d like to know more about these different techniques, you can check out this article.
However, there are lots of different brands of stoneware and earthenware clay. And each brand will have different qualities. For example, Susan Halls (2014) points out that terracotta earthenware is good for hand-building because it has good plastic strength. However, she also explains that white earthenware clay is hard to hand build with because it is very smooth. As a result, it lacks ‘plastic strength’, becomes floppy, and is hard to join.
Similarly, a smooth stoneware that contains fine grog might be easy to use on the potter’s wheel. The smooth texture feels nice as it turns on the wheel. And at the same time, the fine grog helps the clay stay in place once the shape has been formed.
However, not all stoneware clay will behave like that on the wheel. For example, others point out that red stoneware clay gets waterlogged fast on the wheel and tends to collapse easily.
So, it’s hard to make generalizations about which clay is better for a particular way of forming the clay. However, it is possible to make some generalizations about the way different ways that stoneware vs earthenware clay are fired.
Firing Stoneware and Earthenware Clay
The firing of clay to make it into ceramic ware is normally categorized in the following ways:
Temp Ranges | Fahrenheit | Celcius |
Low Fire | 1852-2109 | 1011-1154 |
Mid Fire | 2158-2266 | 1181-1241 |
High Fire | 2316-2377 | 1269-1303 |
The exact temperature range of each of these categories varies according to whom you ask. But generally speaking, the firing ranges are around those specified in the table above.
As mentioned earlier, earthenware clay is a low fire clay. In addition to that, it is usually decorated with a low fire glaze. Low fire glazes melt and coat the pottery in the lower temperature range.
Earthenware clay is low fire for a few reasons. One of the main reasons is to do with a process called vitrification. Clay contains glass-forming materials. And when these ingredients heat up in the kiln, liquid glaze is formed within the clay body. This liquid glaze moves into the pores between the clay particles. As the clay cools down after firing, the glass solidifies and the pores remain sealed. This is the process of vitrification.
Vitrification
Some clay bodies contain more glass-forming materials and become more vitrified and non-porous than others. Earthenware clay does not contain enough glass formers to become vitrified. And this is a reason why it is still porous when it has been fired to maturity. Pottery is said to be mature when it has reached its optimal density and hardness.
Another reason is that vitrification starts at temperatures that fall in the mid-fire range. Because of the impurities in earthenware clay, they usually start to bloat, deform or become brittle in the mid-fire range.
Stoneware, on the other hand, does contain enough glass-forming ingredients to become fully vitrified. In addition to this, stoneware clay can tolerate being fired at mid or high fire temperatures. For that reason, it’s often called mid or high-fire clay. Because of this, the ceramic ware gets hot enough for vitrification to occur. If stoneware clay is fired to maturity, it is described as being vitreous.
Earthenware Vs Stoneware Glazes
The glazes used on earthenware pottery are often brightly colored and have a high sheen. This is partly to do with the lower firing temperature. Bright primary colors survive more effectively at lower temperatures. By contrast, they tend to get burned out at higher, stoneware temperatures.

As a result, colors typically found on stoneware pottery tend to be more organic and natural-looking. It’s a matter of personal taste whether you prefer the bright vibrance of earthenware or the earthy tones of stoneware.
Another difference between earthenware and stoneware glazes is referred to as the ‘body-glaze layer’.
The Body-Glaze Layer
As mentioned above, when glaze is fired, it becomes liquid glass and coats the pottery that it’s been applied to. When a stoneware clay body gets hot enough, it also begins to flux, which means that it begins to melt.
This is the process of vitrification described above. At this point fluxes in the glaze and the clay body mingle and fuse together. The glaze flows into the pores on the surface of the clay. When this happens the glaze and clay become knitted together firmly.
In fact, the clay and glaze have formed an intermediary layer, that creates a strong bond. Pottery that has a strong body-glaze layer is tough and does not chip readily.
By contrast, earthenware pottery does not form an intermediary body-glaze layer. This is because earthenware clay does not flux in the same way as stoneware clay. Instead, glaze tends to sit on the surface of earthenware clay. Whilst the glaze does create a waterproof barrier, it is not as strong, and will chip off more easily.
The tendency for earthenware glaze to chip and crack is relevant to the next section. Namely, whether stoneware vs earthenware pottery is best for dinnerware and ovenware…..
4) Ovenware and Dinnerware
Until around the 1300s, all pottery was made of earthenware. So, ceramics for cooking and serving food was made out of earthenware clay. Around this time, stoneware came on the scene. Stoneware is thought to have first been created in Germany, by potters who fired more refined clay at a higher temperature than usual for the time (source).
So, earthenware and stoneware ceramics have both been used over the years to make and serve food. And this remains true today. Dinnerware and ovenware can be made and bought in both types of clay. This may leave you wondering what are the advantages of one over the other.
Ovenware and dinnerware have to withstand two factors when they are used. These are:
- The knocks and bumps, wear and tear of everyday use
- Extreme, and often sudden, changes in temperature
Therefore, ideally, kitchenware is strong, but not vulnerable to thermal shock. Thermal shock is the stress that ceramic is put under due to sudden changes in temperature. Some ceramics cope well with thermal shock, others will break or shatter.
Is Stoneware or Earthenware Best?
The trouble is that stronger, harder ceramics cope less well with thermal shock than softer more porous ceramics.
Earthenware is porous and weaker than stoneware. This means it does not do too well with the inevitable bumps and knocks in a kitchen.
This would suggest that stoneware was the better option for ovenware and dinnerware. However, a very dense hard piece of ovenware would have a low resistance to thermal shock and may break.
The ideal for ovenware is a ceramic body that is somewhere between the two extremes. For example, earthenware clay can be adjusted to make it denser, and therefore stronger. One way to do this is to add frit to the clay body (source). Frits are a ceramic glass in a powdered form.
Because frit is glass, it boosts the glass-forming material in the clay. As a result, earthenware clay can be encouraged to vitrify and become stronger.
Another alternative is to use stoneware clay. But to avoid firing it to the point where it is as hard and as dense as it can be.
Final Thoughts
When weighing up the pros and cons of stoneware vs earthenware, there are a few factors to consider. To sum up, these are the relative porosity of the ceramic ware and the strength you require in your pottery. But also, the look and feel of the ware are important too. If you are making your own pottery, you will also want to consider what they are like to work with. And also, what temperature your kiln fires at.