Your cart is currently empty!
How to Clean Raku Pottery – Let Your Raku Shine
Published:
Last Updated:
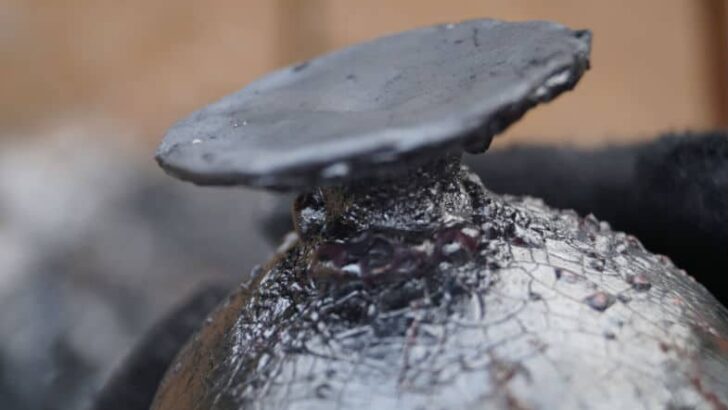
Affiliate Disclaimer
As an affiliate, we may earn a commission from qualifying purchases. We get commissions for purchases made through links on this website from Amazon and other third parties.
There are two occasions when you might want to clean raku pottery. If you have made or bought a piece of raku you might want to know how to keep it dust-free. Or, you may want to know how to clean off the carbon residue left from the firing process. This article is mainly about how to clean raku pottery after it has been fired.
However, I will also discuss how to look after your raku in the long run. Before getting into the nitty-gritty of cleaning your raku, here is an overview of what you need to know.
Carbon and soot can be scrubbed of fired glazed raku pottery. A domestic cleaning powder and a scrubbing pad or nail brush will work. Don’t scrub unglaze parts of the pot and avoid getting cleaning agents on those areas too. A propane torch can be used on stubborn patches of carbon.
Let’s start by looking at how potters recommend cleaning carbon and soot off their newly fired raku pottery. Raku firing can be adrenalin-fuelled. It is dramatic and can be nerve-wracking. When you are gathering your breath after raku firing, you may not want to get on with cleaning your ware.
However, it is an important part of the process. It is only after cleaning off the excess carbon deposits that you get an idea of what you have made. So, though the cleaning of raku can feel a bit unwelcome, the results are worthwhile.
How To Clean Raku Pottery After Raku Firing
There are a few ways that potters allow their raku pottery to cool down after firing. One option is to allow your pottery to cool in the open air. This creates a matte black finish through oxidation. Alternatively, some potters will almost immediately quench their raku ware in water (source). If you use either of these approaches, cleaning your raku after firing is not so much of an issue.
However, often potters remove red-hot pottery from the kiln and nestle it in combustible materials like newspaper or sawdust. The dry material burns and smokes. The raku is placed in a garbage can and covered with a lid. Or it is placed on a pile of combustible material and covered with a bucket.
This creates a reduction atmosphere in which the surface areas of the raku that are not glazed become carbonized. When the pottery is removed from the reduction chamber, it is often covered in burned material. And there will be excess soot and carbon clinging to the surface.
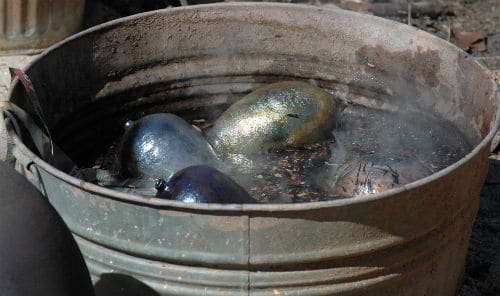
Typically, potters will submerge the pots, which are still hot into water to cool and clean them. This is called quenching. In addition to the crusty bits of carbon, glazed pots will often be covered with a brown film. The flakes, crust, and film can be difficult to remove and can require some elbow grease.
However, there are techniques to clean raku pottery to make the process less arduous. And there are a few things to take into consideration during the cleaning process, so read on…
How to Clean Raku Pottery
How you clean your raku pottery depends on the finish that it has. Some raku is glazed all over. Other raku pottery is partially glazed with areas that are left bare and which become black with carbon.
Then there is naked raku. In naked raku resist slip, or resist slip, and a glaze is applied to the pottery before it’s raku fired. The slip and glaze shrink and crack during firing and when the pottery is removed hot from the kiln.
When the raku ware is sitting in the reduction chamber, carbon settles on the cracked areas of clay. This results in black lines where the bare clay has been exposed. When the pottery is removed from the reduction chamber the slip and glaze flake away. Any glaze that remains needs to be cleaned off. The result is raku pottery that is ‘naked’ but decorated with black carbonized cracks and smoky patterns.
Each of these finishes needs to be handled differently once the firing is over.
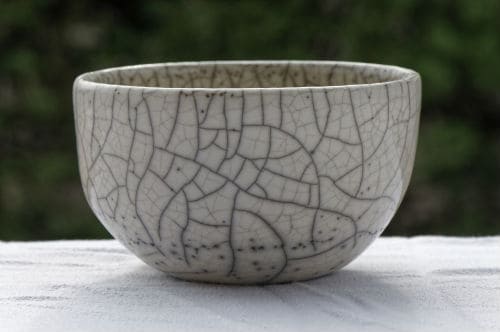
Cleaning Unglazed Raku Pottery
There are a variety of different kinds of glaze used on raku pottery. Some glaze is specifically formulated for raku. However, the glaze you use on raku need not be specific raku glaze.
Regardless of any differences in the kind of glaze you use, raku is a low-temperature firing process. For that reason, glazes on raku pottery are not especially strong. This is one of the reasons raku is not recommended as dinnerware – because it chips and scratches easily.
Nevertheless, even low-fire glaze is tough enough to withstand a bit of scrubbing. And that is what you will need to do to remove carbon and dirt from your fired raku.
So, how do you do this?
There are several techniques used to clean raku pottery. Most of them involve using everyday household products.
An ordinary abrasive cleaning product like Comet or Ajax will do. Bar Keepers Friend is also recommended by potters as being an effective way to clean raku pottery.
Often potters will use a combination of cleaning products. Or they will use them in a particular sequence that has worked for them in the past.
General guidelines about how to clean raku are to wet the pottery and then sprinkle some cleaner on generously. Then using a nail brush, green abrasive cleaning pad, or toothbrush, simply scrub away the soot and debris.
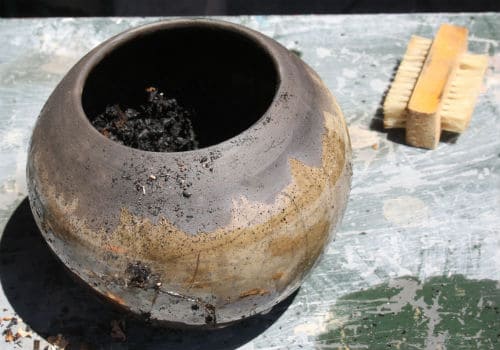
If you don’t want to use commercially produced scouring products, you can make your own. One way to do this is to mix whiting or feldspar powder commonly used in glazes with liquid soap. Then use this as a scrubbing paste with a scrubby pad or some wire wool.
Alternatively, potters sometimes recommend using fine wet sand. This can be used on its own with a scrubbing brush. Or it can be mixed into another one of the above cleaning pastes.
Once you have scrubbed sufficiently to have removed the dirt and carbon, rinse the pottery thoroughly. It’s important to get rid of the cleaning product, otherwise, it can leave a sticky white residue. Also, if it isn’t fully removed, when your pottery dries out it can cause clouding on unglazed areas.
Some potters state that after using a scouring product, they will then use a metal cleaning pad. An example might be Nevr Dull or Brasso Metal Wadding. Alternatively, a brillo pad can be helpful to remove stubborn areas on the raku.
A Dremel tool with a polishing bit on the end can also be used to tackle really caked-on debris.
Be brave, but proceed with caution!
With all of the above techniques, it is good to bear in mind some simple guidelines.
Scrubbing with abrasive powders works well on shiny glazes, especially white crackle glaze. However, be more cautious with glazes that contain a metallic luster as too much scrubbing will remove the luster effect.
Try to minimize cleaning products on unglazed parts of pottery as they can discolor and stain.
Do look at the ingredients in a cleaning product before you use it. Or at least do a test piece to see how it fares with a new cleaning agent. Some ingredients in cleaning products are very abrasive. For example, quartz is more abrasive than glass and may scratch a glazed surface (source)
Remember to rinse, rinse, rinse your raku once you are done cleaning. It’s important to get rid of all that soapy gritty product.
Cleaning Matte Glazes on Raku
Shiny glazes are tougher than matte glazes. Strictly speaking, a matte glaze is a sintered layer, rather than a glaze. As such, matte glaze is softer than a gloss glaze. Matte raku glaze loses its color and depth relatively quickly and can benefit from being sealed and preserved.
Matte glazes also don’t cope as well with scrubbing and cleaning as shiny gloss glazes. So, it is best to avoid scrubbing matte glaze finishes. And especially avoid cleaning them with an abrasive cleaning product.
Using a Propane Torch to Clean Raku Pottery
Some potters recommend using a propane torch to remove carbon residue from glazed raku (source). Carbon and soot are produced when there is incomplete combustion of the materials in the reduction chamber.
The raku pottery goes into reduction when there is insufficient oxygen to burn all the combustible material. As a result, the flame becomes smoky and laden with sooty carbon.
If you gently sweep a propane torch flame over the glazed surface of your raku, the residual carbon burns away. Basically, the propane torch is completing the combustion process that didn’t happen fully in the reduction chamber.
There are a few things to bear in mind about this process:
- Sweep the flame across the pottery. An easy way of doing this is to put your pottery on a banding wheel and turn it gently. If the flame lingers too long in one area it might overheat.
- Use this technique when the pottery is still a bit hot from firing. If you use it on cold pottery the glaze or pottery might crack.
- Don’t use the torch on unglazed areas as it will burn the black carbon surface from your raku.
After Care and Ongoing Cleaning of Raku Pottery
Once your raku pottery is finished, you may want to know how to clean it and preserve its unique character.
Here are a few suggestions for looking after raku pottery once it has been made:
- Avoid putting raku in direct sunlight as this can make the colors fade. If you want to keep it in a sunny area or in the garden, there are ways to protect it. See my article here on how to seal your raku and protect it from UV rays.
- Limit the contact a raku piece has with water. Although there are measures that can be taken to make raku water-resistant, ultimately raku is vulnerable to water. As such it is best to keep its contact with water to a minimum.
- Cleaning ornamental pieces is best limited to dusting with a soft cloth or feather duster.
Final Thoughts
Because raku pottery is a low fire process, it is relatively fragile once fired. However, to clean raku pottery after it has been fired you do need to use some elbow grease. Glazed raku surfaces can be scrubbed with some vigor to reveal the underlying glaze surface. Non-glazed raku surfaces need to be treated with a bit more care in the post-reduction firing process.