Your cart is currently empty!
How Long Does It Take for a Kiln to Cool Down?
Published:
Last Updated:
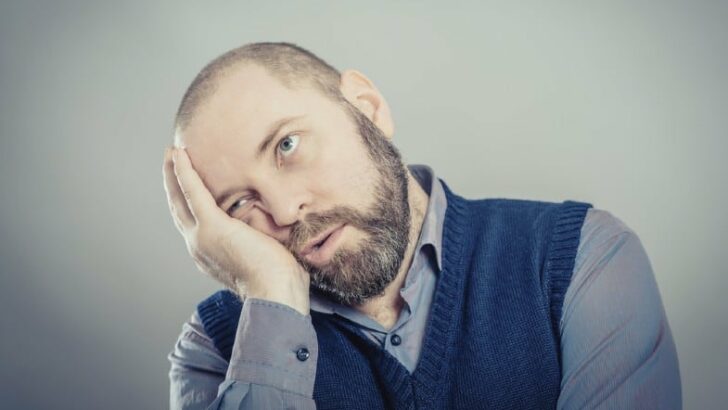
Affiliate Disclaimer
As an affiliate, we may earn a commission from qualifying purchases. We get commissions for purchases made through links on this website from Amazon and other third parties.
Once you’ve made your pottery and fired it you may be desperate to see how it has turned out. You probably want to know how long does it take for a kiln to cool down. This article is about how long you can expect to wait, and what factors affect the cooling time.
The time it takes for a kiln to cool down depends on a few factors. Some of these are the final cone temperature and the size of the kiln. However, the rule of thumb is that cooling the kiln takes at least as long as firing the pottery. So, if it takes 12 hours to reach your target temperature, it takes 12 hours for the kiln to cool.
For clarity, it’s always good to define your terms. And different potters consider different temperatures to be cool. So, let’s have a quick look at what we mean by a ‘cool kiln’.
Waiting for your Kiln to Cool Down – How Cool Does It Need to Be?
If you ask 20 potters what temperature to open your kiln, you will likely get 20 different answers.
Some will tell you that they are happy to lift the lid of their kiln if it’s under 300F. Another potter might be happy to open and unload a kiln with heat-resistant gloves at 200F. Whilst another potter will only consider a kiln to be cool when they can unload the kiln with bare hands.
Waiting for your kiln to cool down, especially after a glaze fire can feel painfully slow. You’re probably desperate to see what your pottery looks like.
I empathize, but really, the lower the temperature you open the kiln, the better. Most potters will recommend that you find ways to fill your time whilst you’re waiting. If you’re hanging around waiting for the kiln to cool down, time will creep by.
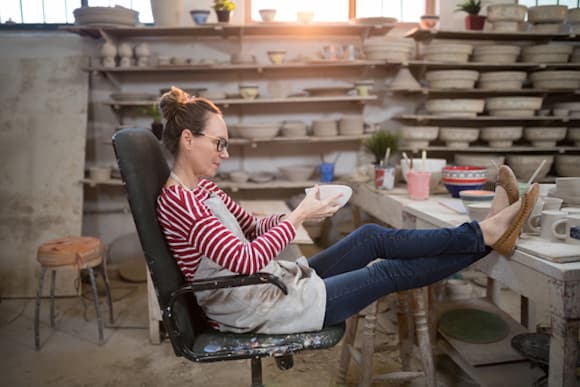
As I will describe below opening your kiln up when it is too hot risks damaging your pottery. And you can lower the life expectancy of your kiln too.
It’s wise to err on the safe side. Some manufacturers, for example, Skutt, will recommend that you wait until the kiln is under 125F before you open the kiln lid. So, for argument’s sake, let’s assume for now, that a cool kiln is 125F or below.
How long does it take to get from your final cone temperature to 125F? Let’s have a look at that question now….
Some Rules of Thumb
Two rules of thumb are often quoted amongst potters about how long it takes for a kiln to cool down. Unfortunately, these general rules contradict one another!
One school of thought states that it takes as long for a kiln to cool as it does to heat up. Another school of thought is that in general, it takes double the time to cool the kiln down.
Why Does the Cool Down Time Vary So Much?
There are a few reasons why kiln cooling times can differ. These factors are:
Kiln Size
Smaller kilns heat up and cool down quicker than larger kilns. There is less volume and mass to cool so they lose heat more quickly.
Ventilation
Kilns with a downdraft ventilation system fire more quickly and cool down more quickly than unvented kilns. Generally, a kiln with a downdraft vent will cool about 1/3 quicker.
Brand of Kiln
Some kilns cool more quickly than others. For example, kilns with thicker insulation take longer to cool down than kilns with thinner walls.
The Type of Clay You Are Using:
The ware you are firing doesn’t affect how much time it takes for the kiln to cool down. However, it does affect whether you can speed the cooling process up.
Some clays, like grogged clay or raku clay, can cope better with changes in temperature. Raku clay, for example, is designed to withstand thermal shock. So, you don’t need to nurse these clays through the cooling process as much as other clay bodies.
How Long Does It Take for a Kiln to Cool Down?
Manufacturers generally state that it takes a kiln as long to cool down as it did to reach top temperature.
The length of time it takes to reach the final cone temperature depends on a few factors. One of these factors is whether you are doing a bisque or a glaze fire.
Cooling Down a Bisque Fire
Bisque fires vary in length depending on the clay you are using, and the model of kiln. However, the average length of a bisque fire is around 12 hours. Some potters find that they bisque more quickly than this. Others will take longer. But as a general principle, 12 hours for a bisque fire is not uncommon.
With that time scale in mind, it will take another 12 hours for the kiln to cool. So, in total, the fire will take 12 hours, and the cooldown will take another 12. As such a realistic estimate is that your bisque fire will take 24 hours from start to unloading your kiln.
Cooling Down a Glaze Fire
As a general rule, bisque fires take a little longer than glaze fires. This is because you are advised to bisque fire slowly.
It’s important during the bisque fire that the organic material and moisture are removed from the clay gradually.
By the time you get to glaze firing, the clay is in a more stable state. As such, you can safely ramp up the temperature in the kiln more quickly, with less risk of exploding your ware.
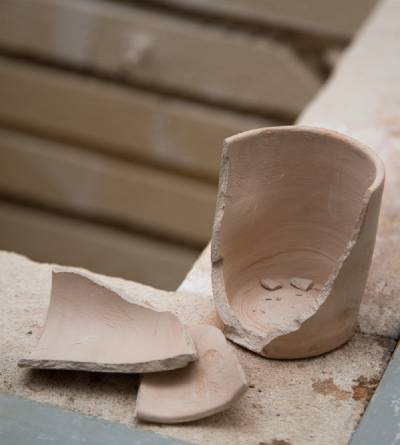
As such, glaze firing the same load may take around 8 hours. Bear in mind that different clay bodies will require different firing schedules. It takes longer to mature a cone 10 clay than it will take to glaze fire to cone 06. So, glazing high fire clay takes longer than low fire clay.
Nevertheless, for simplicity’s sake let’s assume that the glaze fire takes 8 hours. In general, it takes longer to cool down a glaze fire than it does to reach the final temperature.
One of the reasons for that is that the glaze is in a volatile state as it cools. If it cools too quickly it can crack or craze. The glaze needs time to solidify back from its liquified state and for imperfections to heal over. It’s best not to rush this process, or you the glaze can lose some of its radiance.
Therefore, if your glaze fire takes 8 hours, it may take 12 hours for the kiln to cool down sufficiently.
The Bottom Line on Cooling a Kiln
There is a lot of individual variation in the way that potters fire they ware. Potters have different ways of working. One potter firing to cone 10 may take 16 hours to glaze fire and 24 hours to cool down. Another potter may aim to fire for 10 hours and cool the glaze fire in a maximum of 10 hours.
With time, most potters find a time frame for firing and cooling that works for their set up. Nevertheless, however long it takes to get your kiln to temperature, it will take as long to cool down. This is the bottom line. You may choose to cool down more slowly than this, but the reality is that cooling a kiln takes time.
The best thing you can do is find a way of occupying yourself during that period. Otherwise, the wait can feel interminable.
Controlled Cooling
Most of the time potters leave their kiln to cool naturally. The kiln reaches its top temperature in the firing schedule and then turns off after a short period of soaking. After the soak, the temperature in the kiln naturally begins to slowly drop.
However, it is possible to slow the cooling process down. This is a technique used by potters who want to achieve a kind of crystal formation in particular glazes. Some specialist glazes, called macro-crystalline glazes, form very beautiful crystal effects when cooled slowly.
Some digitally controlled kilns can be programmed to cool down at a rate that’s slower than the natural cooling rate. It’s a bit trickier, but not impossible to do controlled cooling if your kiln has a kiln sitter. Check out this really handy video by EvolutionStoneware on controlled cooling with a kiln sitter.
Speeding Up the Kiln Cooling Process
More often than not, potters want to know how to cool down their kiln more quickly.
Here are some of the ways that potters will speed up the cooling process:
- Cracking the lid of the kiln toward the end of the cool-down process
- Taking the plugs out of the peep holes
- Using a box fan to circulate air around the kiln
- Installing a downdraft ventilation system
Whilst these are common practices, it’s important that you don’t try to cool the kiln too quickly or too early.
Ceramics goes through something called the quartz inversion around 1064F (573C). This is a small but sharp expansion in volume. The quartz inversion happens as the clay heats up during firing, and also as the clay cools down.
It’s important that the firing and cooling schedule is happening slowly at the point of the quartz inversion. It is a stressful time for the clay and it can’t be rushed through this particular window in the schedule.
In addition to the quartz inversion, it’s important to avoid your ceramics undergoing thermal shock.
This is what happens if there is a sudden rapid drop in temperature. The ceramics will shrink very rapidly, which puts it under too much internal tension. As a result, it may crack. Thermal shock can occur if the lid is cracked too early, or the peep holes are opened too soon.
Thermal shock can also affect glazes, causing your glaze to craze. Or generally spoiling the overall finish of your glaze.
Final Thoughts
The reality is that it takes a long time for a kiln to cool down. There are ways that you can speed up or slow the cooling process down somewhat. Different potters will report different cooling times. But, however long it took to heat your kiln, you can expect it to take as long to cool down.